All in one labelling machine
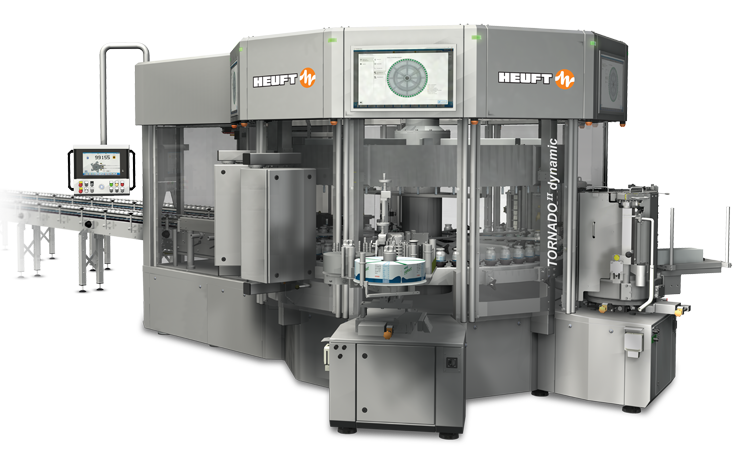
HEUFT TORNADO II dynamic
Genuinely responsive labelling results: semi-modular labeller with voice control.
The HEUFT TORNADO II dynamic has an open design and is a semi-modular machine based on the highly automated HEUFT SPECTRUM II which achieves simply more performance, dynamics and precision when applying wet glue, self-adhesive and wrap-round labels with up to four flexibly integrable labelling stations and incorporated quality inspection. Its innovative dialogue function for a hands-off voice control creates real responsivity during machine analysis and process monitoring for full efficiency and productivity all along the line.
Camera-based, servo-controlled container adjustment
Aligning with millimetre accuracy: approximate and fine alignment for a high-precision label application.
Creases and bubbles, misalignment and offset: one of the up to four permanently assembled, easy to replace stations in the HEUFT TORNADO II dynamic without a machine table is equipped with two high-performance cameras, which are safely enclosed and automatically adjustable in height, for the approximate and fine alignment of the cylindrical food jars or bottles to be labelled in order to prevent labelling faults such as these from occurring in the first place. They use inconspicuous container structures such as mould seams or embossing as reference points for the precise servo-controlled rotation of each container so that the labels are applied tidily and without creases with millimetre precision where they belong.
Read more...
The container-specific rotating cam is no longer controlled mechanically but electronically due to the use of the practically wear-free HEUFT TORNADO II flex servo technology. This makes them programmable according to the brand so that brand changes function almost fully automatically and completely without replacing cam segments. Servomotors in the dispensing head carry out a high precision distribution of the labels from the roll during self-adhesive labelling.
Fullscreen
Wet glue labelling
Applying precisely: exact complete equipment.
Accurately, gently and tidily: the HEUFT TORNADO II dynamic can be equipped with one or more electrically coupled wet glue stations for, among other things, body, collar or neck ring and closure labelling depending on the application. The containers are sent past them after they have been transferred to the carousel and fixed by the centring elements. At the same time the integrated glue segments are covered with an exactly adjustable quantity of glue so that each one of them picks up precisely one label whilst passing.
Read more...
A gripper cylinder then pulls it off and presses it gently with the glued side against the precisely aligned food container. A sponge ensures a homogeneous application. The servo-controlled labelling platforms rotate the containers harmoniously so that the wet glue labels are applied tidily and brushed on without creases. The optionally available automatic magazine feed (see below) ensures that their supply does not run out too quickly and prevents unwanted production stops.
Fullscreen
Wrap-around labelling
Rotating harmoniously: a precise application all around.
PA perfect fit, carefully and without an offset: special units can be integrated into one or more of the four labelling stations of the HEUFT TORNADO II dynamic easily and flexibly for wrap-around labelling – with individually controllable nozzles which apply fine spots of glue in the right quantity and exactly to the jars or bottles fixed in platforms by means of centring bells. A servo-controlled belt drive rotates the containers harmoniously at a speed which can be specifically regulated for different formats so that the labels can wrap themselves around them completely and precisely.
Read more...
The glue spots which have been applied pull the labels out of the magazine. At the same time a special nozzle applies a thin line of glue to the end of the label for the final gluing so that the overlap can be stuck precisely, practically without an offset, and brushed on carefully. A closed hot glue system keeps glue consumption low and prevents contamination. This reduces maintenance costs and increases operational reliability during the accurate application of wrap-around labels.
Fullscreen
Self-adhesive labelling
Applying accurately: perfectly sticking labelling results.
Dynamic, precise and accurate: corresponding units, with which one or more labelling stations in the HEUFT TORNADO II dynamic can be equipped, apply self-adhesive labels exactly. The containers enter the labeller if the container stop which stops the production flow in the case of a malfunction is unlocked. The infeed worm ensures that the gap between them is correct in the course of this before they are taken over by the infeed starwheel and transferred to the machine carousel. This is exactly where the self-adhesive labels are applied precisely and with a close fit.
Read more...
The roll with the labels is placed in the labelling unit with servo-controlled dispensing head for this purpose. Thus they can be peeled off at the dispensing plate and applied to the passing containers using special pads. They are firmly clamped for this – in fact centrally between the rotating platform and the centring bell. Therefore nothing can slip and the labels remain stuck exactly where they belong.
Fullscreen
Integrated quality check
Checking labelling results: fault detection in the same work process.
Its open design without a machine table gives the semi-modular HEUFT TORNADO II dynamic optimum accessibility and above all plenty of room for the application-specific integration of the most varied technologies, procedures and modules. Many other quality control technologies can also be integrated into the new generation labelling machine in addition to wet glue, wrap-around and self-adhesive labelling and the camera casing which can be swivelled out for a fine container alignment for particularly accurate labelling
Read more...
In this way intelligent colour sensor cameras check, among other things, their presence, position and brand affiliation immediately after the labels have been applied so that incorrectly labelled jars, tins or bottles which cannot be marketed can be rejected directly. These are by no means all the additional functions (see below) which are made possible by the uncomplicated integration of proven HEUFT detection modules in one and the same work process with the careful labelling.
Fullscreen
Fault rejection
Preventing recalls: the reliable rejection of faulty containers.
Fast, careful and accurate: highest precision when detecting faults is only effective if the products in question are also removed afterwards. The single-segment and multi-segment rejection systems of the HEUFT rejector series deal with this both precisely and carefully.
Easy brand changes
Changing over without tools: straightforward adaptation with audiovisual assistance.
Highly automated, uncomplicated and fast: the manual effort for the user is kept to an absolute minimum when changing programs to other container brands. The height and position of the machine head adapts just as automatically to the changed container format as do the alignment cameras and detection modules. The same applies to the servo-controlled rotating cam which can be programmed according to the brand and is therefore reproducible at any time so that the time-consuming mechanical replacement of individual cam segments is not necessary. The significantly reduced proportion of change parts can be replaced without tools. The innovative voice dialog function (see below) informs the user in good time when a brand change is due or initiates it directly upon his verbal instructions.
Read more...
The HEUFT NaVi user guidance provides audiovisual step-by-step assistance in order to implement the few manual interventions competently. The tidy user interface which is not only displayed on the terminal of the compact labelling machine but also on four flat screens positioned around its upper part provides a complete overview. And the HEUFT checkPoints which flash conspicuously help actively to locate those hardware components exactly where something needs to be done. The open design which is practically without a machine table ensures optimum accessibility. This means that brand and program changes as well as retrofitting can be carried out quickly and easily.
Hands-off voice control
Simply responsive: efficient dialog function.
Attractive, responsive and efficient: the new generation semi-modular labeller can be operated without any manual intervention and by voice alone in a real dialog with Amanda the virtual assistant – via Bluetooth headsets. Amanda listens to the user, answers questions and speaks to him of her own accord as soon as something needs to be done. For example he hears in good time how many labels are still in the magazine or how long the respective program still needs to run. Verbal instructions for actions such as brand changes or test container programs are implemented directly. The innovative hands-off voice control always keeps the user informed about the situation of the labeller and the entire process in clear language and protects against losses in performance, failures and downtimes actively. This creates full responsivity during machine analysis and process monitoring and sustainably increases the efficiency and productivity of entire filling lines.
Fullscreen
Central lubrication
Greasing automatically: reduced maintenance.
Central, automatic and economical: the correct amount of grease is applied to all the moving parts of the labelling machine so that everything always runs like clockwork. The integrated central lubrication system greases the main bearings and the rotary gears for the container platforms and an oil pump the labelling stations. A special labyrinth seal prevents water entering the closed oil system in the course of this. This ensures the durability of all the components sustainably. Complex maintenance work can therefore be dispensed with.
Fullscreen
Optional additional functions
Making even more possible: extensions to the range of functions.
The labelling machines with their modular design based on the highly automated HEUFT SPECTRUM II with multi-processing capabilities can be expanded at any time. Thus the range of functions of the HEUFT TORNADO II dynamic dynamic can be optionally extended with numerous additional functions for optimising and checking the labelling and product quality.
Read more...
For example the automatic magazine feed (AMF), with which one of its four stations can be equipped, makes a non-stop labelling operation possible. The servo-controlled add-on module increases the label stock during the wet glue labelling process and therefore minimises the need for manual intervention: a new magazine is pushed into place automatically during running operation when a magazine is empty. Standstills are therefore sustainably avoided and human resources effectively saved. Different technologies, among other things, for a burst bottle detection, internal container pressure measurement, fill level detection, closure inspection, logo, BBD and code verification can also be integrated directly into the easily accessible machine in addition to the above-mentioned camera modules for checking the presence and position of the label. The optionally available clean in place function saves time and supports the employees because it cleans the labelling stations automatically without the time-consuming dismantling of individual components.
Fullscreen
HEUFT SPECTRUM II
Simply automating: universal device platform for maximum performance.
Highly automated, universal and powerful: the HEUFT SPECTRUM II ensures optimum detection and operational reliability during an in-line quality assurance for the sustainable safeguarding of product quality and line efficiency.
Read more...
The cross-system control unit with multiprocessing capability for different modules, systems and applications convinces due to its exceptional degree of automation. Brand and format changes can be carried out without manual intervention. The unique human machine interface of the universal device platform is self-explanatory. Human resources are effectively saved in this way. In-house developed hardware and software of the latest generation and a future-proof network connection achieve highest computing power and data transmission in real time. The result: maximum precision during purposeful product tracking, inspection and rejection.
Fullscreen
HEUFT NaVi
Simply knowing what to do: self-explanatory audiovisual user guidance.
Intuitive, individual and audiovisual: previous knowledge is not required in order to operate the HEUFT SPECTRUM II systems reliably. The HEUFT NaVi user guidance is self-explanatory and supports the respective user step by step.
Read more...
An RFID login with user-related access rights provides an overview and makes the respective user's work simply easy: he only sees what he really needs to on the clearly arranged touchscreen user interface with a flat menu structure, integrated tutorials and precise auxiliary tools in order to fulfil his specific tasks optimally. He is supported by a virtual assistant in the course of this. She speaks to him and clearly explains what has to be done when and where. Purposeful and focussed on the essentials – the audiovisual HEUFT NaVi user guidance makes the reliable operation of HEUFT systems simply easy!
The innovative hands-off dialog function creates additional added value during process monitoring, analysis and voice control of the new generation labelling machine.
Fullscreen
HEUFT checkPoints
Simply seeing where what has to be done: trouble-free localisation.
Clear, direct and purposeful: the user can cope immediately on the rare occasions when manual intervention is needed. Because eye-catching HEUFT checkPoints make it clear at a glance exactly when it is necessary to take matters in hand in addition to the audiovisual information which the HEUFT NaVi provides. The orange tags with clearly assignable letters are on the device components where intervention may be required. If the worst comes to the worst the HEUFT NaVi shows them on the touchscreen. The HEUFT checkPoints then even optionally flash on the respective component in each case. The problem is located without a long search. This saves time and human resources, shortens standstills and therefore increases productivity.
Open, flexible and durable construction.
Simple maintenance and straightforward retrofitting: optimum accessibility.
Compact, semi-modular and versatile: the HEUFT TORNADO II dynamic is the first labelling machine based on the highly automated HEUFT SPECTRUM II to have a construction without a machine table which provides plenty of space for flexible equipping and retrofitting. Up to four electrically coupled labelling stations can be easily integrated into one and the same machine. Three wet glue units for the collar, back and neck labelling of up to 60,000 containers per hour are just as possible as a combination of wet-glue, self-adhesive and wrap-around labelling including including a camera-based, servo-controlled fine alignment of the containers or AMF. Even then the open design, without a bulky machine table, still provides sufficient space for integrating further modules and components – whether for the direct detection of labelling faults and many other impairments to the packaging and product quality or for an automatic clean in place system.
Read more...
Optimum accessibility is always guaranteed during cleaning and maintenance work. For example, the casing of the alignment cameras can be easily swivelled out in order to perform such tasks unhindered, quickly and carefully. The machine itself is made of stainless steel and galvanised components. All the moving parts of its low vibration construction are extremely durable. The rubber parts of the glue segments are vulcanised and dimensionally stable, the centring heads are practically wear-free and the centring bells are easy to replace. All the components which come into contact with the containers are made of plastic. This keeps the noise level of the labelling machine which has been constructed for optimised maintenance at the lowest level.
HEUFT CleanDesign
Cleaning quite simply: hygiene-optimised construction.
Accessible, clean and safe: its HEUFT CleanDesign predestines the system for use in hygienically sensitive areas.
Read more...
Sloping surfaces facilitate cleaning and prevent the accumulation of stubborn dirt. Special channels and openings allow the liquids required for cleaning purposes to be drained off completely. Consequently dangerous germs and bacteria have no contact surface whatsoever. Specially constructed casings and doors create optimum accessibility. The electronics are totally encapsulated. Sensitive areas such as the inspection units are dust-proof and protected against contact as well as water jets.
Network technologies
Networking everything: online connection for increased efficiency and quality.
Information transmission in real time, production data acquisition, line analysis and remote maintenance: networking is the answer!
Read more...
HEUFT systems have future-proof network interfaces (Gigabit Ethernet and TCP / IP) for an online connection via the Internet and the database interface (SQL / DDE) for top line efficiency and an optimum quality management with considerably faster and easier workflows. Therefore production data, shift records, productivity faults and HACCP limit value analyses are available network-wide. The result: early identification of quality and efficiency problems. The firewall protected direct connection to the HEUFT TeleService makes competent remote maintenance possible all around the clock.
HEUFT rejector
Removing faulty products: the right rejector for all cases.
The labelling machines from HEUFT can be equipped with different rejectors depending on the application. For example, the single-segment HEUFT flip and HEUFT mono rejectors as well as the multi-segment HEUFT DELTA-K and HEUFT DELTA-W systems are ideally suited for rejecting faulty full containers with the HEUFT TORNADO II dynamic..
- semi-modular all-in-one machine of the new generation for high-precision wet glue, self-adhesive and wrap-around labelling
- flexible equipping or retrofitting with up to four stations for a camera-based container alignment, individual labelling and automatic magazine feed
- easy to integrate inspection modules for sustainable quality assurance for full containers
- powerful HEUFT SPECTRUM II platform and HEUFT TORNADO II flex technology for servo-controlled rotating cams which can be programmed according to the brand and are reproducible at any time, accurate labelling results as well as simple, almost fully automatic brand changes
- open design without a machine table for optimum accessibility during changeovers, cleaning and maintenance work
- compact, robust, low-wear construction in accordance with the hygiene-optimised HEUFT CleanDesign
- audiovisual HEUFT NaVi user guidance and innovative hands-off voice control for full overview, responsivity, operational reliability, efficiency and productivity
- online connection for production data acquisition and remote maintenance
- performance range – up to 1,000 containers per hour