Full case inspection
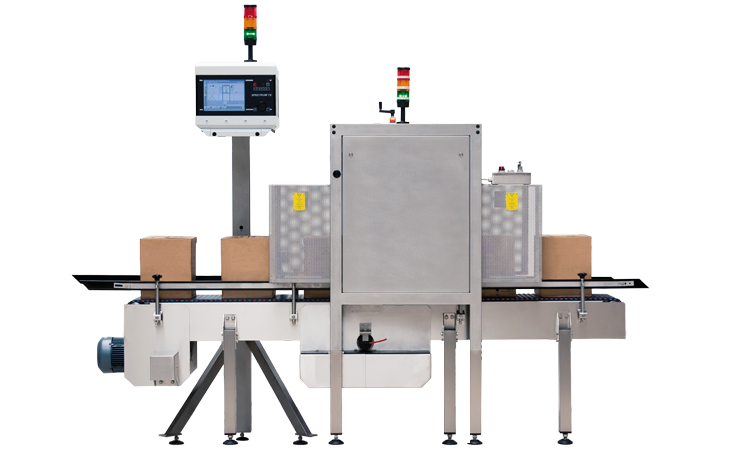
HEUFT GX
Checking outer packaging specifically: precise full case inspection.
The HEUFT GX checks the quality features of the newly packed outer packaging of pharmaceutical containers such as trays and cardboard boxes. It identifies deformations, raised cardboard box flaps, incorrect colours and logos just as reliably as missing units inside the case.
Shape check
Ensuring transportability and unpackability: detecting distorted cases.
Stackable, transportable and functional: full cases should be in top shape. Otherwise they cannot be stacked, transported or stored. Furthermore distorted cases and cardboard boxes make it difficult to remove the containers contained in them. Therefore the HEUFT GX only allows outer packaging to pass which is in top shape. It checks its dimensions and measurements for this using sensors. The full cases in question are removed before being loaded if these deviate from the specifically determined limit values.
Cardboard box flap check
Detecting raised flaps: checking they are closed.
Falsely positioned, raised and incorrectly closed: this not only looks unsightly if this is the case with regard to the flaps of cardboard boxes for drinks. In addition the effectiveness of the outer packaging and the safety of the sensitive contents contained in it are at risk. Therefore the HEUFT GX checks the position of the flaps and that they fit correctly ensuring that the complete case is closed. Sensors scan its edge areas for this. The measured values change if they are covered by raised flaps. Thus the respective outer packaging is detected reliably.
The rejection of faults
Preventing recalls: the reliable rejection of faulty cases.
Fast, careful and accurate: highest precision when detecting faults is only effective if the products in question are also removed afterwards. The device either emits a conveyor stop signal or activates the corresponding rejection system, such as the HEUFT xcase, in order to remove incomplete cases from the production flow.
Product monitoring and self-tests
Playing it safe: exact product tracking and regular self-tests.
Always knowing the current location of a particular product: each one is tracked precisely for this. This ensures that none remain uninspected.
Read more...
The integrated reject verification checks that each product identified as faulty is really removed. Standard test programs guarantee a regular examination of the detection performance. Network-based continuous documenting and long-term archiving of the results.
Simple brand changes
Changing automatically: automatic adjustment of the detection units.
Reliable, uncomplicated and easy: the HEUFT GX carries out brand changes without manual intervention. All the parameters are adapted automatically and the height and position of the detection units adjusted by motor. This practically rules out misadjustments saving valuable time and money.
Optional additional functions
Making even more possible: extensions to the range of functions.
The HEUFT GX with its modular design can be extended at any time. Thus the following additional functions, among other things, can be integrated:
- A special camera system reliably differentiates between different case colours for highest brand purity. Three measuring windows can be determined for this so that differently coloured promotional stickers and symbols do not distort the result.
- The reliable detection of non-brand logos is also achieved optically. Up to seven different logos can be photographed and compared to the stored original in this way.
- The precise detection and differentiation of barcode labels is carried out by a special sensor system.
HEUFT SPECTRUM TX
Controlling centrally: one platform for all requirements.
Precise, network-compatible and cross-system: the HEUFT SPECTRUM TX forms the basis for different technologies, modules and functions. The devices of the generation of the same name can be exactly adapted to individual requirements on site and retrofitted at any time due to this universal platform.
Read more...
A cross-system component equality of 70 per cent ensures a high availability of spare parts. The central HEUFT SPECTRUM TX control unit creates a high level of precision during continuous product tracking and quality assurance due to its multiprocessing capability. A future-proof network connection ensures reliable remote maintenance and production data acquisition for optimum efficiency and productivity. In-house developed hardware and software and its own operating system ensure computing power and offer no opportunity for viruses or malware.
HEUFT reflexx
Combining photographs and reliably detecting objects: image processing in real time.
Fast, powerful and exact: combining several camera and X-ray images with each other and specifically detecting various objects. The HEUFT reflexx carries out all this in real time.
Read more...
The in-house developed hardware and software provides high computing capacity and is exactly tailored to the requirements of the in-line quality inspection. It generates high-resolution, noiseless detection pictures and analyses them precisely. Integrated filter technologies clearly differentiate between supposed and actual faults. This reduces the false rejection rate sustainably.
HEUFT PILOT
Operating HEUFT systems reliably: graphical user interface with practical tools.
Clear, helpful and specific: the HEUFT PILOT graphical user interface convinces due to an easy to understand, multilingual menu structure with extensive auxiliary tools. Therefore the reliable operation of the HEUFT SPECTRUM TX systems is not difficult.
Read more...
Important information and clear error messages with service notes provide the respective user with specific support. This avoids incorrect adjustments and shortens standstills e.g. during brand changes. Password protected operator levels adapted to the respective area of responsibility also contribute to this. Also integrated: a complete online user manual and a tool for the uncomplicated identification and direct ordering of spare parts.
Fullscreen
Network technologies
Networking everything: online connection for increased efficiency and quality.
Information transmission in real time, production data acquisition, line analysis and remote maintenance: networking is the answer!
Read more...
HEUFT systems have future-proof network interfaces (Gigabit Ethernet and TCP / IP) for an online connection via the Internet and the database interface (SQL / DDE) for top line efficiency and an optimum quality management with considerably faster and easier workflows. Therefore production data, shift records, productivity faults and HACCP limit value analyses are available network-wide. The result: early identification of quality and efficiency problems. The firewall protected direct connection to the HEUFT TeleService makes competent remote maintenance possible all around the clock.
Removing faulty cases
The right rejector for all cases.
Discharging, rejecting and distributing: HEUFT rejection systems for packaging remove faulty crates, cardboard boxes, trays or shrink wrap packages reliably from the production flow. They achieve maximum performance optimally matched to their respective task with regard to precision and carefulness.
- The HEUFT xcase guarantees brand purity in the bottling hall. Its load-dependent control system which adapts the force of the rejection impact to the weight of each individual case removes non-brand and faulty bottle crates smoothly from the filling line. Crates of varying weights are therefore each rejected an equal distance.
- The HEUFT xtray removes damaged or faulty trays with full containers from the line. For this three rejection fingers which are on a sledge installed under the roller conveyor are extended. Trays can also be distributed onto several lanes if several of these intelligent case rejectors are lined up next to each other.
- The HEUFT maxi-flip rejects empty, half-full or completely full cases each an equal distance onto parallel conveyor chains. Its rejection segment is activated for a longer time in the case of heavy crates or cardboard boxes than for lighter ones. A complex mechanical changeover for different types of cases is not necessary.
- The HEUFT maxi-laner is a space-saving alternative to the HEUFT maxi-flip. The compact system which is installed directly above the conveyor is also impressive with a load-dependent control system. It always rejects crates of different masses and varying weights equally. Distributing the cases onto three lanes is also possible with the HEUFT maxi-laner.
- continuous quality assurance of filled outer packaging
- precise examination of up to 120 full cases per minute
- uncomplicated integration into existing lines
- fully automatic brand changeovers
- simple upgrading and retrofitting due to modular design
- compact, easy to clean construction
- online connection for production data acquisition and remote maintenance with the HEUFT TeleService