Empty bottle sorting
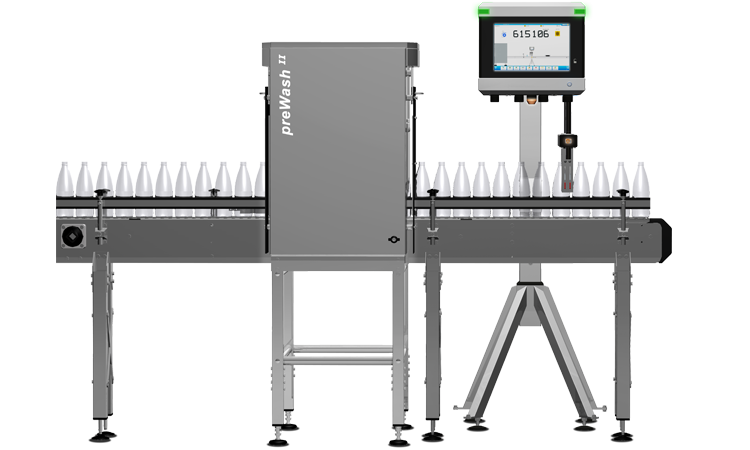
HEUFT SPECTRUM II SX
Simply sorting out: the early detection and rejection of unsuitable empty returnable bottles even before they are cleaned.
Unstable, non-brand, misshapen and contaminated: the HEUFT SPECTRUM II SX with its HEUFT preWash II module detects returning empty bottles with such defects and removes them before they lead to standstills in the washing machine and downstream devices which slow down productivity and can endanger the safety of the end product.
An approximate infeed check
Preventing malfunctions: sorting out unstable empties immediately.
Extremely misshapen, unstable and oversized: empty returnable bottles which cannot be reliably transported, examined and filled in an upright position after they have been unpacked should be detected and rejected before the actual pre-wash inspection. This is only possible if the bottles are stable and upright on the conveyor. The bottles are therefore first checked for overly severe deformations ultrasonically in the infeed of the compact stand-alone solution based on the highly automated HEUFT SPECTRUM II. The optional integration of a special photocell also makes a targeted height check possible. Severely distorted containers lacking stability are therefore already detected and rejected before they can enter the HEUFT preWash II unit.
Residual liquid and closure detection
Sorting out bottles which are sealed and not empty before washing: optical sensor detection.
Not completely empty, still sealed and not to be cleaned: remnants of the original beverage in the returnable bottle or contamination by other liquids such as varnish or lye counteract the cleaning performance of the washing machine. The same applies to empty bottles which are still sealed. It is then impossible to effectively clean the inside of the bottle. Therefore both an IR fill level detection and a closure detection using sensors are directly connected to the central HEUFT SPECTRUM II control terminal of the compact stand-alone system.
read more...
Residual liquid is detected precisely with this and results directly in the rejection of the respective container as soon as its quantity exceeds a certain limit value. Exactly the same procedure is used for empties which are still sealed with closures. Therefore only containers reach the washing machine which can be cleaned completely, safely and without interference. This effectively protects against failures and standstills and ensures the cleaning performance when washing bottles as well as the efficiency and productivity of entire returnable filling lines.
Camera based shape, equipment, contamination and foreign object detection
Showing the contour and identifying the colour: incident and transmitted light inspection.
Non-brand, contaminated and too dirty: the HEUFT SPECTRUM II SX has a total of six high-performance cameras for an all-around sidewall inspection in addition to the modules for checking the fill level and closure which are assembled directly at its central machine human interface in order to also remove such empty bottles before they can enter the washing machine. This HEUFT preWash II detection unit not only photographs the appearance but also the condition of each individual bottle using specific lighting technologies safely accommodated in a space-saving casing directly at the conveyor:
Read more...
the contour inspection using the transmitted light procedure verifies the shape and height so that severely distorted and oversized bottle are sorted out reliably. Even highly soiled and scuffed bottles or those contaminated with foreign objects can therefore be detected and rendered harmless. The colour camera inspection using the incident light procedure identifies label remnants as well as embossing, imprints and ACL labels on the body, back and neck of the empties which do not match the brand actually being produced in order to ensure a homogeneous supply. Furthermore it is also possible to detect their colour in addition to the precise determination of the quantity of residual liquid in order to ensure that bottles with particularly critical contents are rejected even when their quantity is below the respective limit value. Only bottles of the correct type which can be cleaned, inspected and filled reliably pass the HEUFT preWash II module of the HEUFT SPECTRUM II SX. This protects against standstills and increases the efficiency and output of entire returnable filling lines.
Fault rejection
Preventing recalls: the reliable rejection of faulty containers.
Fast, careful and accurate: highest precision when detecting faults is only effective if the products in question are also removed afterwards. The single-segment and multi-segment rejection systems of the HEUFT rejector series deal with this both precisely and carefully.
Fullscreen
Product monitoring and self-tests
Playing it safe: exact product tracking and regular self-tests.
Always knowing the current location of a particular product: each one is tracked precisely for this. This ensures that none remain uninspected.
Read more...
The integrated reject verification checks that each product identified as faulty is really removed. Standard test programs guarantee a regular examination of the detection performance. Network-based continuous documenting and long-term archiving of the results.
Fullscreen
Easy brand changes
Adapting automatically: self-acting and assisted format changes.
Brand and format changes are the order of the day in modern beverage filling plants. The higher-level control unit of the HEUFT SPECTRUM II preWash already has an unprecedented level of automation and support for the user in order to carry them out quickly, easily and without errors. In this way the position and height of the detection modules adapt automatically to the changed container format. The HEUFT NaVi user guidance provides the user with audiovisual step-by-step assistance which not only makes brand changes simply easy.
HEUFT SPECTRUM II
Simply automating: universal device platform for maximum performance.
Highly automated, universal and powerful: the HEUFT SPECTRUM II ensures optimum detection and operational reliability during an in-line quality assurance for the sustainable safeguarding of product quality and line efficiency.
Read more...
The cross-system control unit with multiprocessing capability for different modules, systems and applications convinces due to its exceptional degree of automation. Brand and format changes can be carried out without manual intervention. The unique human machine interface of the universal device platform is self-explanatory. Human resources are effectively saved in this way. In-house developed hardware and software of the latest generation and a future-proof network connection achieve highest computing power and data transmission in real time. The result: maximum precision during purposeful product tracking, inspection and rejection.
Fullscreen
HEUFT reflexx A.I.
Simply detecting more: real-time image processing with artificial intelligence.
The AI discipline of machine learning for targeted object classification has been mastered by our self-developed image processing since 2010! And since then it has learned a lot: intelligent filters distinguish drops of water on the container from air bubbles in the glass and even make it possible to identify tiny defects which are hidden behind ACLs or embossings. HEUFT reflexx A.I. now also uses deep learning!
Read more...
Appropriately trained neural networks are used for example to denoise X-ray images or to find dangerous foreign objects in structured products and to reliably distinguish them from good objects which are extremely similar in their shape, size and density. With true artificial intelligence, the hardware and software from our own development and production again increases detection reliability - and minimises the false rejection rate. The smart image processing can be directly integrated into the HEUFT reflexx A.I. camera which was developed in-house and which processes and evaluates its own images directly in real time and raises the adaptive image analysis to a top level.
Fullscreen
HEUFT NaVi
Simply knowing what to do: self-explanatory audiovisual user guidance.
Intuitive, individual and audiovisual: previous knowledge is not required in order to operate the HEUFT SPECTRUM II systems reliably. The HEUFT NaVi user guidance is self-explanatory and supports the respective user step by step.
Read more...
An RFID login with user-related access rights provides an overview and makes the respective user's work simply easy: he only sees what he really needs to on the clearly arranged touchscreen user interface with a flat menu structure, integrated tutorials and precise auxiliary tools in order to fulfil his specific tasks optimally. He is supported by a virtual assistant in the course of this. She speaks to him and clearly explains what has to be done when and where. Purposeful and focussed on the essentials – the audiovisual HEUFT NaVi user guidance makes the reliable operation of HEUFT systems simply easy!
Fullscreen
HEUFT checkPoints
Simply seeing where what has to be done: trouble-free localisation.
Clear, direct and purposeful: the user can cope immediately on the rare occasions when manual intervention is needed. Because eye-catching HEUFT checkPoints make it clear at a glance exactly when it is necessary to take matters in hand in addition to the audiovisual information which the HEUFT NaVi provides.
Read more...
The orange tags not only flash on the touchscreen but also at the respective component if the worst comes to the worst. The problem is located without a long search. This saves time and human resources, shortens standstills and therefore increases productivity.
Network technologies
Networking everything: online connection for increased efficiency and quality.
Information transmission in real time, production data acquisition, line analysis and remote maintenance: networking is the answer!
Read more...
HEUFT systems have future-proof network interfaces (Gigabit Ethernet and TCP / IP) for an online connection via the Internet and the database interface (SQL / DDE) for top line efficiency and an optimum quality management with considerably faster and easier workflows. Therefore production data, shift records, productivity faults and HACCP limit value analyses are available network-wide. The result: early identification of quality and efficiency problems. The firewall protected direct connection to the HEUFT TeleService makes competent remote maintenance possible all around the clock.
Compact construction
Space-saving integration: full detection in a confined space.
The high-performance camera technology of the HEUFT preWash II module is in an extremely space-saving casing which can be placed directly at the conveyor beside the central HEUFT SPECTRUM II control unit with the modules for a liquid and closure detection. This makes the solution for pre-inspecting and sorting empty bottles a particularly space-saving, flexibly integrable compact system. Therefore ensuring full detection and rejection reliability in the long term in the tightest of spaces.
-
timely sorting out of unsuitable empties
-
effective protection against problems and standstills of the washing machine and downstream systems for full line efficiency and productivity
-
reliable detection and rejection of non-brand, distorted, sealed, heavily soiled and highly contaminated empty bottles
-
space-saving stand-alone system
-
safely encased lighting and camera technologies for full detection reliability on the running conveyor
-
HEUFT reflexx A.I real-time image processing with learning ability for detailed fault detection and reliable differentiation of the most varied objects
-
highly automated HEUFT SPECTRUM II platform with self-explanatory HEUFT NaVi user guidance
-
automatic adjustment of the detection units during brand and format changes
-
online connection for remote maintenance and production data acquisition
-
performance range – up to 72,000 empty bottles per hour